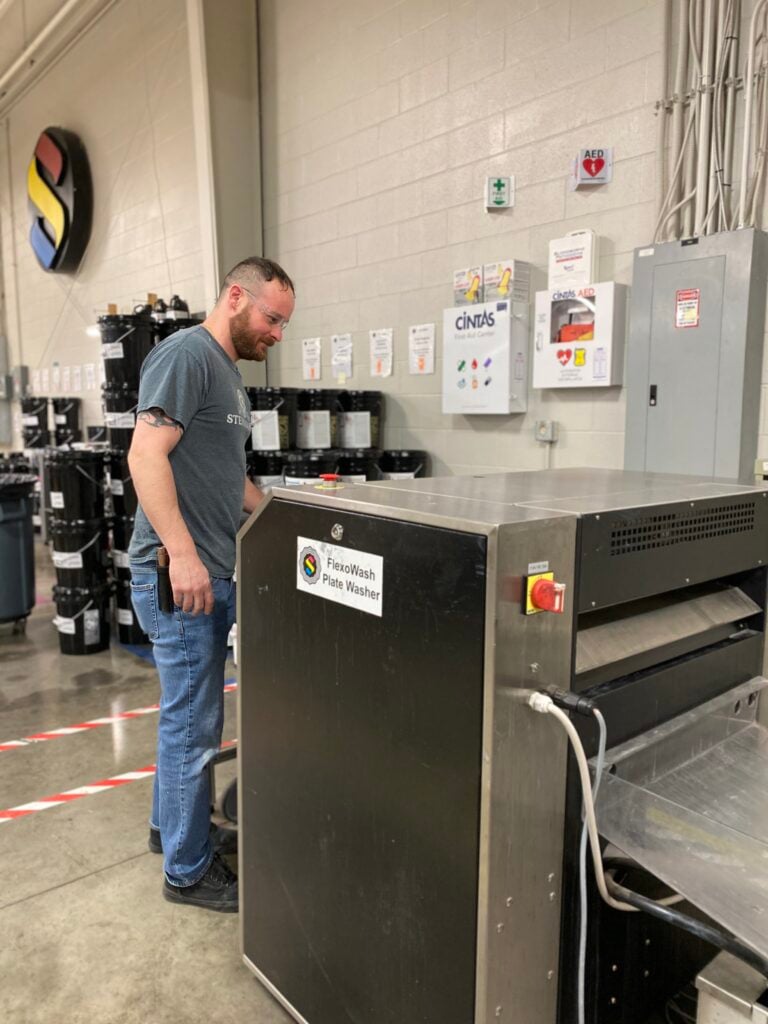
Eight months.
Eight months was all it took for Steinhauser to get a complete return on their investment in their FW Plate Washer.
But more than the return on investment, they got their time back as well. And most importantly, they got gratitude from their employees. As Steinhauser CEO Tara Halpin states “It is amazing how thankful our guys are to have these tools available to help them do their job more effectively.”
Here’s their story:
Steinhauser is a well-known fourth generation family owned narrow web printer located outside Cincinnati, Ohio. They have two Narrow Web Flexo Presses. They were already a Flexo Wash customer with a Flexo Wash Anilox Cleaner, but their cleaning needs were not all completely solved. They were manually washing their flexo plates BY HAND and it had become a daunting task.
According to Halpin, Steinhauser realized that they could not do manual washing anymore when they “were having a significant number of remakes of plates and the costs were through the roof. Simultaneously, the process we were using was not effective, was a safety hazard and was causing excess cleanup around the presses.”
Their Manual Plate Washing Statistics BEFORE:
- About 30 plates were cleaned per day and it took three minutes to clean each plate by hand.
- They did not have the manpower to keep up and they spent 90 minutes each day cleaning plates manually.
- Plates were getting damaged, causing additional downtime on the press. Roughly 26 times a year, a damaged or dirty plate would take the press down, which took about 1.5 hours to fix.
- These plates were getting damaged during cleaning. Furthermore, with 100 lost plates a year at a cost of $120 each, the financial expense had a definite impact on the bottom line.
ROI Became the Deciding Factor on the Purchase
When Steinhauser and Flexo Wash began talking about the FW Plate Washer, Flexo Wash calculated their Return on Investment immediately and determined that it would pay for itself in eight months. According to Halpin, ROI “was the deciding factor for me. When my team brought it to my attention and I saw the numbers, I knew we had to make the purchase.”
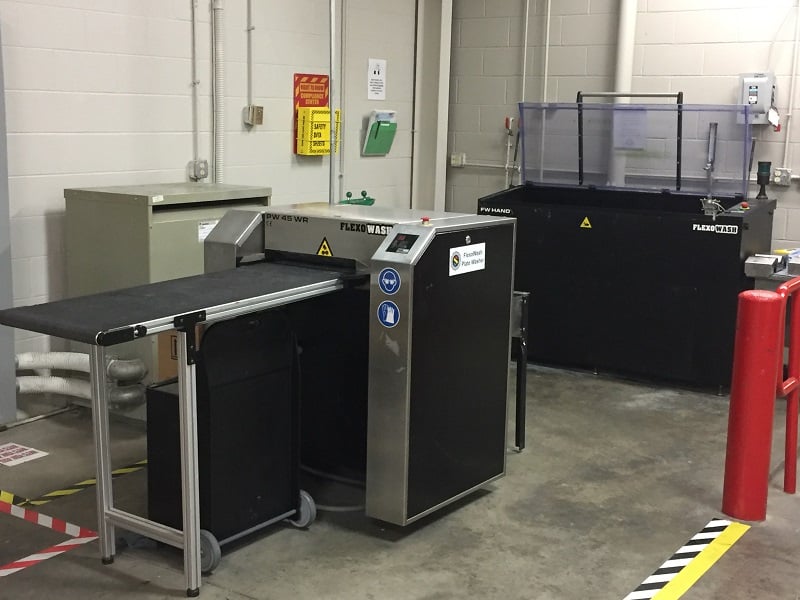
Their Plate Washing Statistics NOW, Since Using the FW Plate Washer:
- They clean 40 to 50 plates a day, depending on the workload.
- They do NOT have a dedicated person for this job. They use a Press Helper from each press to clean the plates.
- The people who previously did the manual cleaning were the Pressman and the Helper. Now the Helpers run them through the Plate Washer at their convenience. “This has provided us with a reduction in make ready times and contributed to an upward trend in uptime as well.” according to Chris Wermes, Pre-Press Operations Manager at Steinhauser.
- They save “easily” four to five man-hours a day.
- They have basically eliminated all washing-related plate damage.
In retrospect…
Halpin states that “When I saw it run, it was just so simple that I could not believe we did not invest in the technology sooner.” She also has a sense of humor about her prior cleaning processes: “When we think back to the way we cleaned plates before our Flexo Wash Plate Washer, we literally laugh out loud. The image of a handmade spindle over a barrel to hold the plate on its cylinder while the pressman cleans it with alcohol and sprays it dry with an air hose, comes to mind.”
Lesson learned, and Halpin adds that “this piece of equipment has been a game changer for our flexo team”.
IN CONCLUSION:
Halpin knew that as a high-volume production label converter that she would need to increase her production while still keeping her employees at optimal productivity and performance. She has done this effectively by creating a positive work culture at Steinhauser, giving her employees all the tools they need to succeed and be confident in their work.
In regards to the FW Plate Washer, she says “I cannot imagine running a print facility without one. The efficiency it creates for your press crews, the reduction in make ready times, damaged plates and the appreciation you will get from your team makes it a no brainer.”
Most of all, her employees love using it. “We talked to our pressmen and helpers and they continue to be thrilled that we brought the technology into our plant. It is easy to use and maintain, it produces a much cleaner plate and there is confidence that the plates will be in perfect shape to run the next time. “
The Flexo Wash Plate Wash systems are designed according to the type of printer and type of ink used. All models will wash the polymer plates within only a few minutes and the unique design and function make it extremely easy-to-use for the operators. There’s minimal maintenance, and the job gets done safely and on schedule with less fuss.
“We like to support our customers so that they eliminate downtime and are more productive. We know that when an operation like Steinhauser runs smoothly day-to-day the profitability of the entire company goes up. Even incremental changes can affect the bottom line. That’s why a plate washer purchase often makes sense,” said Patrick Potter of Flexo Wash.
Flexo Wash serves all sectors of the label and package printing industry with installations around the world. Today, the Flexo Wash portfolio includes laser and liquid anilox cleaning, plate and plate sleeve washing, rotary screen cleaning technology, as well as the original parts washing machines. It has more than 4,000 machines in everyday commercial use worldwide.