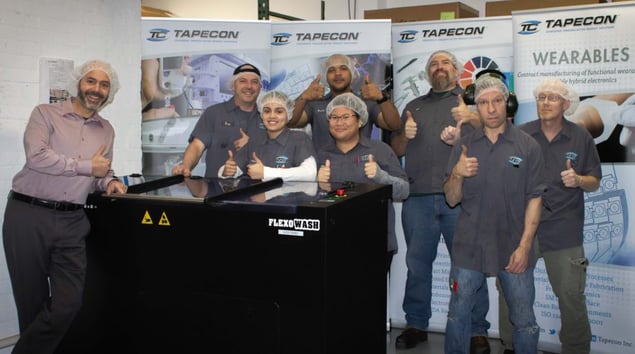
TAPECON MEETS FLEXO WASH
With all the great successes and production increases in their business, Tapecon needed to expand their print quality processes as well. They turned to Flexo Wash back in 2007, wanting to clean their anilox rolls more efficiently and thoroughly without damage or increased downtime on press. They purchased a single roll Flexo Wash Anilox Cleaner and saw increases in their productivity immediately.
That single station Anilox Cleaner served them well but their business was growing. With a growing company, growing printing needs and more changeovers, they once again turned to Flexo Wash and bought a FW Handy 2×2 Anilox Cleaner, large enough to clean four anilox rolls at a time.
Here are some statistics of their results:
- They print 253 days a year.
- They used to spend 15 minutes cleaning per roll, with setup and placement.
- Now they spend about two minutes cleaning each roll, and that includes walking time to get the cylinders out of the printer to the cleaner.
- Cleaning supply cost is too minimal to categorize
Beyond this data, the bigger results are the most telling to Tapecon. They utilize the 6M Method of Cause and Effect Analysis in all of their operational processes: Manpower, Materials, Measurements, Mother Nature, Methods and Machines.
If any person or process is down for 15 minutes, they write down the name, date and issue and post on a public message board that gets addressed weekly by a group of Tapecon engineers. They analyze and solve the problem, using this 6M process.
Since the purchase of the new FW Handy 2×2, dirty anilox has never come up as a problem. “This is a testimony to the new system because before, it was a pain point” according to Director of Operations, Michael Gerbera. Their Flexo Wash cleaner is able to clean their obscure inks off their anilox with success.
He described his new Flexo Wash system with a common analogy: If you walk into a messy room, you realize it’s messy. If you walk into a clean room, you don’t realize it’s clean and that’s because you expect it to be clean. That’s the way it is when the anilox cleaning system is working. You expect it to work and for your anilox rolls to be clean. It just works and you expect that every time.
Tapecon is committed to data and process improvement. They are always looking for new ways to grow and develop. They are also committed to improvement. Flexo Wash was their solution to their pain point of dirty anilox rolls, too much downtime and reduction of productivity. Flexo Wash was the right technology at the right time. Flexo Wash is committed to improvement as well.
Bottom line:
Flexo Wash is a piece of the bigger puzzle for Tapecon. Constant evolution and growth has been the key to this company that has stayed in business and remained a relevant, industry leader for a century. With their commitment to investing in their company, keeping it ahead of the curve with the implementation of the latest technology and a forward-thinking company culture, Tapecon will be here for another century as well.